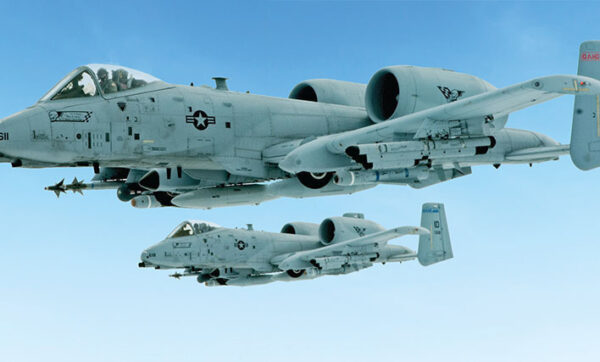
Editor’s Note: This article was originally published in the March 2018 issue of JED. To read past issues in full, visit our magazine archive.
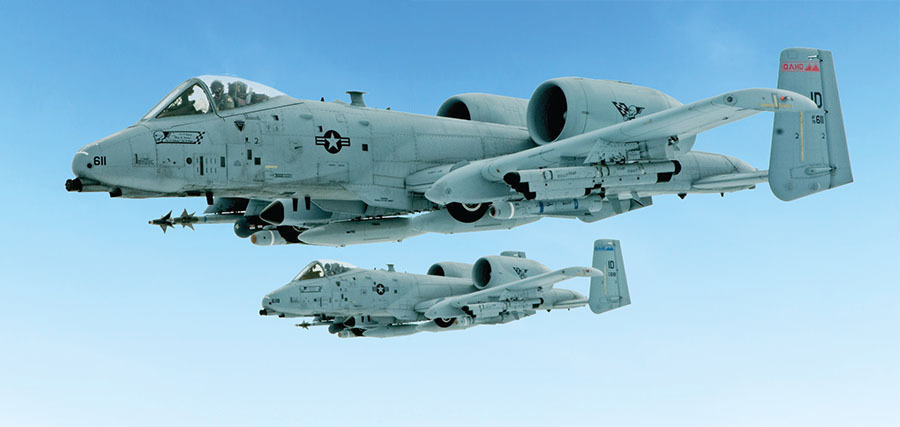
At 7:55 a.m. EDT on September 15 of last year, NASA’s Cassini spacecraft plunged into the planet Saturn’s atmosphere, transmitting a final set of science observations to Earth from its 20-year voyage of discovery through the solar system including a 13-year tour of the ringed planet itself.
The joint Cassini-Huygens mission represented a tremendous scientific achievement for NASA, the European Space Agency (ESA) and the Italian Space Agency. The wealth of data and new knowledge of the solar system it provided will be invaluable, as will the lessons learned in benefit of future manned and unmanned space exploration. There is, however, one other important lesson clearly demonstrated by the Cassini spacecraft that may not be as immediately appreciated.
Nearly all of the RF systems on Cassini were powered with traveling wave tubes (TWTs), including science research instrumentation, telemetry and control, and its data link back to earth. Launched in 1997, there was major debate at the time of its development whether its systems should be built not with vacuum tube technology but with solid-state amplifiers, an argument based largely on the perception that tube technology was unreliable. As it turned out, however, arriving at Saturn in 2004, NASA extended Cassini’s mission twice – first for two years, and then for seven more, unquestionably proving the viability and reliability of Cassini and its tube-technology-based systems over a 20-year, deep-space environment lifetime.
TWTS CRITICAL TO NEXT-GENERATION REQUIREMENTS
Today, the tube vs. solid-state competition continues apace with reliability questions often still cited by advocates of the latter. But, as Dr. William Devereux (Dev) Palmer, (at the time of this interview, program manager at the Defense Advanced Research Projects Agency’s Microsystems Technology Office), points out, “In truth, if you look at the debates that have gone on over tubes and solid-state electronics over the decades (and in fact one of the reasons that it has gone on for so long), you’ll see that it usually centers around the outer edges of the power/frequency design space.” The history of this, as described by Palmer, can be seen in the evolution of technology aimed at meeting the requirements of the time for operation in the microwave region of the spectrum. “Before GaAs [gallium arsenide]transistors began to become useful in the microwave space, the only solution was tubes. Then, GaAs began to displace tubes at lower frequencies, but there were still always applications that wanted to stay ahead of the commercial electronics market, which meant pushing further out in frequency and power-generation capabilities.” And, this (leading-edge) domain, says Palmer, “is always going to be the domain of the vacuum power tube.”
Outlining the discussion in general terms, Palmer says this is because TWTs have two principle advantages over solid-state systems. The first is that the tube’s vacuum operating environment itself means that the electron-transport process doesn’t involve electrons bouncing against a semiconductor lattice and generating heat, and thus limiting their efficiency in terms of the power vs. heat-generation equation. Also, TWTs incorporate a device known as a “multistage depressed collector” that captures the energy from the spent electron beam and recycles it back it into the system to further increase the efficiency of the amplifier as a whole. Palmer points out that this (power-generation efficiency) is one of the primary reasons that vacuum tubes are particularly popular for space-based applications. “Any time you decrease the power efficiency of an amplifier, you increase the size of the power supply required, which means you can therefore generally make the size of an overall system smaller by using a vacuum tube.”
A HIGH-POWER PATH TO THE MM-WAVE BAND
The truth of the view that leading-edge applications are the “domain-of-the-tube” can be seen today with the growing interest in reaching further and further into the millimeter-wave band (30-300 GHz) of the spectrum. Located between the microwave and IR frequency spectrums, mm-wave is in increasingly high demand, particularly for defense applications with the greater throughput demands being placed on data links overall, and more specifically with the growing use of UAVs. Says Palmer, “Generally speaking, you want to operate in clear air, where other people aren’t already operating, and millimeter-wave offers you the opportunity to do that. And, it’s also efficient at transmitting large amounts of data at high speed. To do this, you need an especially high power, very linear amplifier, like you get from vacuum electronics.”
Another reason that TWTs are of particular interest for millimeter-wave applications is that as applications move up in these frequencies, atmospheric absorption gets much higher than that found at lower frequencies. As a result, says Palmer, “If you want to put a certain amount of power on target or close a link, you need a bigger amplifier. So, as you push out higher into the millimeter-wave arena, you’re also upping your power axis to get sufficient transmit power to do what you want to do.”
DARPA PROGRAMS ADDRESS NEXT-GENERATION VED TECHNOLOGY
Initially launched within DARPA’s Microsystem Technology Office, and now transitioned to its Strategic Technology Office (STO), the High-Power Amplifier using Vacuum electronics for Overmatch Capability (HAVOC) program is investigating “revolutionary approaches in the development and demonstration of a new class of compact, high-power, and wide bandwidth millimeter-wave vacuum electronic devices (VEDs) capable of linear amplification in a form factor compatible with mobile and airborne platforms.”
The term “overmatch” basically refers to being able to generate higher power RF signals than other systems competing for the same millimeter-wave band space, providing significant advantage to friendly users. HAVOC is one of two major DARPA efforts launched to dramatically improve the capabilities and manufacturability of vacuum tube technology.
Phase 1 HAVOC contracts were awarded in May of 2016 to Communications & Power Industries LLC (CPI) Microwave Power Products Division (Palo Alto, CA); L3 Electronic Devices (Williamsport, PA); and Northrop Grumman Mission Systems (formerly Electronic Systems) (Linthicum, MD) for work on developing high-power, wide band millimeter-wave amplifier tubes.
Funding for HAVOC is divided between Basic Research (PE 0601101E R-1 Electronic Sciences) and Applied Research (PE 0602716E ELT-01 Electronic Technology). Basic research funding for HAVOC in both FY2017 and FY2018 was set at $5 million, while Applied Research funding levels were set at $18 million for both years.
According to the budget request document, basic research work covers the development of compact RF signal amplifiers for air, ground, and ship-based communications; sensing; and radar systems operating at millimeter-wave frequencies above 75 GHz. Aimed at “improving our understanding of the various phenomena governing vacuum electronic amplifiers operating at mm-wave frequencies above 75 GHz,” HAVOC focus areas will include modeling and simulation techniques, advanced manufacturing methods, novel beam-wave interaction structures, high current density and long-life cathodes. For FY2018, plans call for verifying and validating the performance of high-fidelity, three-dimensional, multi-physics, numerically efficient modeling and simulation techniques on structures representative of advanced vacuum electronic amplifiers; and the fabrication and test of wideband and high-power beam-wave interaction structures, and high current-density cathodes.
Applied research work is aimed at the creation of a new class of wideband, millimeter-wave, high-power vacuum electronic amplifiers, with size, weight, and power (SWaP) features consistent with reusable airborne and mobile platforms. As stated in the FY2018 budget document, “the HAVOC amplifier will provide leap-ahead capabilities to air, ground, and ship-based communications, sensing, and EW systems, but will require significant advancements in cathodes with high current-density and long lifetime, beam-wave interaction circuits with wide bandwidth and high power handling capability, wideband and low-loss vacuum windows, and compact magnetic structures for electron beam transport.”
Goals for FY2018 include the design, fabrication, and test of wide bandwidth vacuum windows with high power handling capability, the investigation of new magnetic materials and magnet configurations that enable compact, integrated beam focusing and transport architectures; and the integration of components into prototype amplifiers for initial testing.
INNOVATIVE VACUUM ELECTRONICS
The second major DARPA initiative in advanced vacuum electronics technology is the Innovative Vacuum Electronic Science and Technology (INVEST) Program. The purpose of INVEST is to strengthen the science and technology base for an entire new generations of vacuum tubes. This includes fundamental research in physics-based modeling and simulation of VEDs, innovative component design, electron emission processes, and advanced manufacturing.
As described by Palmer, “The INVEST program is based on the observation that applications have been moving to higher frequencies all along, and there’s no reason to expect that to stop. The next window that people are looking at is W-band – 94 GHz or so (W-band is 75-110 GHz), and when you get up to those frequencies, the dimensions of the vacuum tools and all of the components (such as high-current-density cathodes, tiny vacuum envelopes, and microparts that extract the RF signals amplified inside the component), get really small, and ultraprecise alignment is even more difficult and critical. As you push frequencies up, you can’t use conventional manufacturing techniques anymore.”
To address this challenge, the INVEST program is looking at ways to use new, more-advanced manufacturing approaches, such as “additive manufacturing.” (Additive manufacturing refers to a process by which digital 3D design data is used to build up a component in layers by depositing material.) For example, says Palmer, “What if you could take an engineering drawing of a tube and ship it to a 3D printer and have the printer just print the entire vacuum tube structure and take care of the precision and alignment at the same time. Indeed, an ultimate and most welcome outcome would be to transform the new scientific understanding and engineering know-how that emerges from the INVEST program into novel tools for analyzing, synthesizing and optimizing new VED designs and then deploying innovative advanced manufacturing methods, including 3-D printing, to actually produce the devices. That is a beautiful vision.”
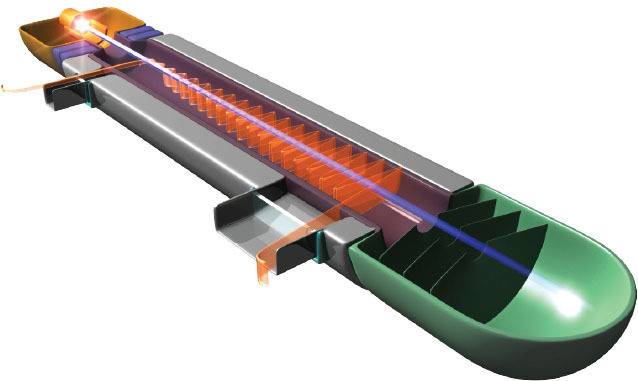
DARPA MTO released a BAA for the INVEST program in August of 2015, and has since awarded a number of contracts to industry and academia to research techniques and technologies. Among these is a program at the University of California, Berkeley (Berkeley, CA) which is looking at additive manufacturing in pure copper.
Palmer also points to multiple projects underway examining ways to improve basic thermionic cathodes. “Thermionic cathodes have been the workhorse that we’ve been using in electron tubes ever since the Fleming valve,” (From Wikipedia – the Fleming valve, also called the Fleming oscillation valve, was a vacuum tube, or ‘thermionic valve,’ invented in 1904 by John Ambrose Fleming as a detector for early radio receivers used in wireless telegraphy. It was the first practical vacuum tube.), but people still don’t really have a thorough quantitative understanding of how and why they work the way they do.”
To address this area, INVEST includes a broad team of universities and US cathode manufacturers looking at the chemistry and material science behind thermionic cathodes and trying to relate this to the manufacturing process and ultimately to performance. Among these are Ohio University (Athens, OH), which is looking at barium-oxide scandium-oxide cathode science and technology, and the University of Kentucky Research Foundation, which is conducting a theoretical and experimental investigation of scandate cathode composition. On the industry side, Ceradyne Inc. (Costa Mesa, CA), is working on fast warm-up scandate cathodes using additive manufacturing, and Leidos (Reston, VA), is modeling the effect of manufacturing tolerance on device performance and yield. Says Palmer, “At some point, maybe we can actually have an a-priori design of a thermal cathode that operates exactly the way we expect it to.”
Another INVEST team from the University of Wisconsin-Madison (Madison, WI) is looking at other compounds besides the common oxides used in cathodes or even some of the newer scandium oxide cathodes to see if there are any other material combinations that might provide better performance. To do this, they’re using a computer modeling technique called “density functional theory” (DFT) to scan the periodic table for compounds that have the lowest “work function” – a critical parameter of a thermionic cathode, in that it defines the temperature required for the thermionic material to emit electrons.
Other researchers are exploring new and different beam-wave interaction structures where the actual amplification occurs through the exchange of energy between the electron beam and the electromagnetic signal. “We’re looking at some new and different ideas for how to build this interaction structure that may not be quite as limited by the geometry,” says Palmer. Among these are the Massachusetts Institute of Technology (MIT) (Cambridge, MA), which is examining the photonic bandgap structure for an oversized and overmoded vacuum electron device.
A wide and disparate list of other activities are being sponsored to pursue other critical VED technology objectives. Among these are work at Teraphysics (Cleveland, OH) on an ultra-compact E-band TWT; RTI International (Research Triangle Park, NC) on a nano-gated emitter array; eBeam Inc. (Beaverton, OR) on an ultra-compact electron gun for oxide cathodes; and the University of New Mexico (Albuquerque, NM) on a clamp clystron for simple construction at high frequency.
COLD-CATHODE TWTS
Perhaps one of the most promising technologies being explored through INVEST is the science of cold-cathode technology. The cathode is the thermionic emitter of the electron beam that flows through the vacuum tube when it is heated to extremely high temperatures (approximately 1,000°C.) The lower the temperature that the cathode material will emit is reflected in its work function which, as described above, is dependent on the material used.
Obviously the lower the cathode temperature requirement, the more efficient and reliable will be the tube, with the “Holy Grail” being a cathode that operates at ambient temperature. This would not only eliminate the need for a heater, but also the time required to warm it up.
In his 2012 IEEE Spectrum article entitled “The Quest for the Ultimate Vacuum Tube,” Carter Armstrong, vice president of engineering at L-3 Electron Devices, says, “Cold-cathode vacuum devices would usher in a new generation of ultra-compact, high-fidelity, highefficiency amplifiers, which could be used, for instance, in powerful yet tiny RF transmitters on small satellites.”
One approach to cold-cathode beam emission is the application of a strong electric field at the surface between the emitter and the vacuum. This inwarddirected electric field exerts an outward force on the electrons and lowers the barrier at which electrons will be released. With most existing technologies, however, such a “field emission” approach would require massively high voltage levels. Nanofabrication techniques are seen as offering a solution to the problem. Since the strength of an electric field between two conducting electrodes gets stronger as the electrodes are brought closer together, by shrinking emitter features to nanometer scales, the field-emitter enhancement can be increased dramatically, allowing for operation at much lower voltages.
Two teams are looking at cold cathode technology as part of DARPA’s INVEST program. MIT is exploring silicon nanowire field emission cold cathodes, while SRI International (Menlo Park, CA) is further exploring “Spindt” field emission cold cathodes. Says Palmer, “(Cold cathode technology) is the technology of the future. If you can actually get a cold cathode that is robust enough to withstand a tube environment, it would simplify the design of the tube greatly. Right now, you effectively have to design a tube that can hold a thousand degree hot rock in the middle of the electron gun and not have everything move too much when it heats up and cools down. If you could instead get a cold cathode, that would be a big step forward.”
LEAP AHEAD TECHNOLOGY
Both the HAVOC and INVEST programs are dramatically forward looking in terms of the technologies they are exploring and developing, and although, as Palmer says, it’s not DARPA’s role to invest directly in support of the manufacturing industry, “it certainly does play a role in calling attention to the need for a manufacturing base capable of bringing these technology capabilities to reality. And, not just the capabilities of the technology today, but also enabling continuous advancement of vacuum electronics in the future as we keep moving up in frequency. You could work on this stuff your entire life and if you’re lucky you’ll get to the point where you can really understand how it works and appreciate the capability.”